Cracking the Efficiency Code: Unveiling De-Bottlenecking Strategies for Effective Assessment and Solutions
Author: David Nguyen
In the complex worlds of mine concentrators and refinery plants there are countless variables that can impact efficiency and productivity. Whether you’re in the business of producing raw materials, concentrates, or refined products, one thing remains constant: the need to identify and eliminate bottlenecks. It’s the age-old question we all strive to answer: how can we do more?
This blog aims to highlight the approach adopted by our teams at Wave International and delve deeper into the realm of well-practised de-bottlenecking process even though inherently all models are wrong, but some are useful. We unravel the process, from its initial proof-of-concept work to traditional de-bottlenecking techniques.
1. DETERMINE — Define the Scope, Gather the Inputs
Define. As with any engineering scope it always bodes well when it is well defined. De-bottlenecking can take on many forms, from performance optimisation of operating equipment to large scale process improvements. A focuse
d engineering effort, driven by clear and concise goals, results in outstanding outcomes.
When defining a scope for de-bottlenecking it is important to recognise if previous de-bottlenecking activities or updated engineering designs have been compartmentalised to the detriment of intended operation. In layperson terms have previous attempts to improve efficiency been too focused on the sum of the parts rather than the whole and therefore, does the scope needs to encompass a wider extent than perceived.
Inputs. Once the goals have been defined, the next step is to determine the inputs. To determine the inputs for the de-bottlenecking process, you first need to consider the timing influences. This means looking at factors such as planned and unplanned maintenance time, available operating time and any delays or idle time. By understanding these time-related factors, you can identify where the bottlenecks in the system may be.
2. DESIGN — Model the Systems, Validate the Information and Test the Boundaries
Model. Once the scope has been defined and the inputs drawn together it is time to evaluate the system in a model. There are many ways to model a system from specific modelling software to excel spreadsheets but as the analogy goes, a model is only as good as the inputs, and to that extent one does not just need good platform to work within but an environment that can manipulate the data, and is simple enough to use, understand, visualise, and present.
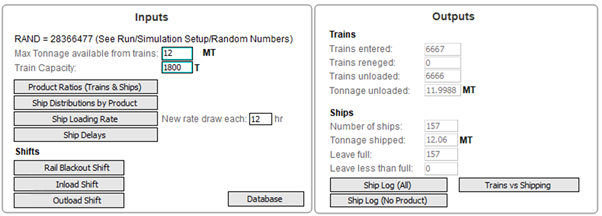
Figure 2 1 – Sample of Model Inputs and Outputs Summary
Validate. As with any form of modelling it requires validation, validation, and more validation. The more effort spent here will ensure less difficulties further down the de-bottlenecking rabbit hole. With the Internet of Things and an infinite number of sensors in a plant there should be ample amounts of data that could be used to validate a model. One advantage of effectively validating a model is that often it can help narrow down the root cause for the bottleneck, or the very least identify an area of which focus should be.
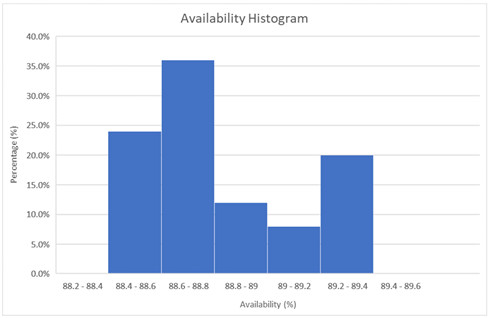
Figure 2 2 – Sample of Validating Plant Availability Taking into Account MTBF and MTTR
It is key to note that validation is not only about validating a model and data, but also historical fact checking equipment capacity via design sizing calculations, and assumptions.
Boundaries. Another aspect of validation is pushing a system/model to the limits. By doing this, it can be evident what can be achieved/not achieved in the process. De-bottlenecking solutions do not always lie on the boundary of limits but if it isn’t understood where the limits of the system are then the results cannot be rationalised.
3. DELIVER — Explore the Options and Optimise the Solution
Optionality. It is important investigate different scenarios inside of the boundaries, there is not always one path to the solution. If done well enough the previous steps in defining and determining the systems would have guided the process to look at other potential pathways.
Optimisation. Once the system is understood from the scope to the inputs, to the model, to its limitations and options, then optimisations can be made. Here is where the goal of debottlenecking comes to the forefront of the process. Keep optimisations simple, it is easy as engineers to over engineer. Just like goal setting keep optimisations S.M.A.R.T. Specific, Measurable, Achievable, Relevant, and last but not least Time bound. Use time effectively to optimise the solution, if it doesn’t work, it doesn’t work! This statement holds true if validation and boundaries have been applied correctly.
Not all debottlenecking projects will lead to a desired outcomes but more often than not, a good outcome will lead to further discussions on where to spearhead the approach. The figure below represents a de-bottlenecking process through stockpile and logistics management to achieve more throughout.
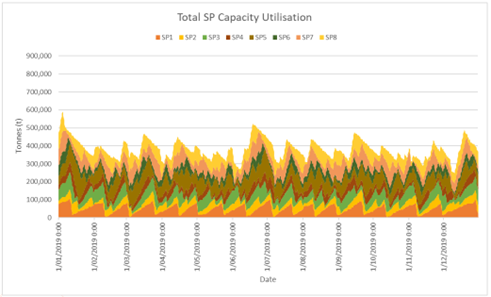
Figure 3 1 – Sample of Stockpile De-bottlenecking Outcomes
Conclusion
De-bottlenecking requires a holistic approach, and this strategy is deeply rooted in our core philosophy of Determine, Design and Deliver. De-bottlenecking is a crucial process for operations looking to improve efficiency, increase production or answering plant capacity queries. A well-established de-bottlenecking process that is well practised offers several key benefits including access to a specialised team, proven processes and tools, and peripheral vision to identify overlooked issues.
Our team at Wave International is fully committed to our clients and their projects, actively seeking the best methods to deliver our work. We understand that diverse perspectives lead to better solutions, and we encourage everyone to contribute their ideas. If you are considering exploring your plant’s performance and looking to improve your operations, contact us today. Let us help you work through the challenges and achieve long-term success.
Stay informed about our latest releases by following our LinkedIn page. By following us, you will receive notifications whenever we publish a new article in the “Resourceful Future” series.
Back to News